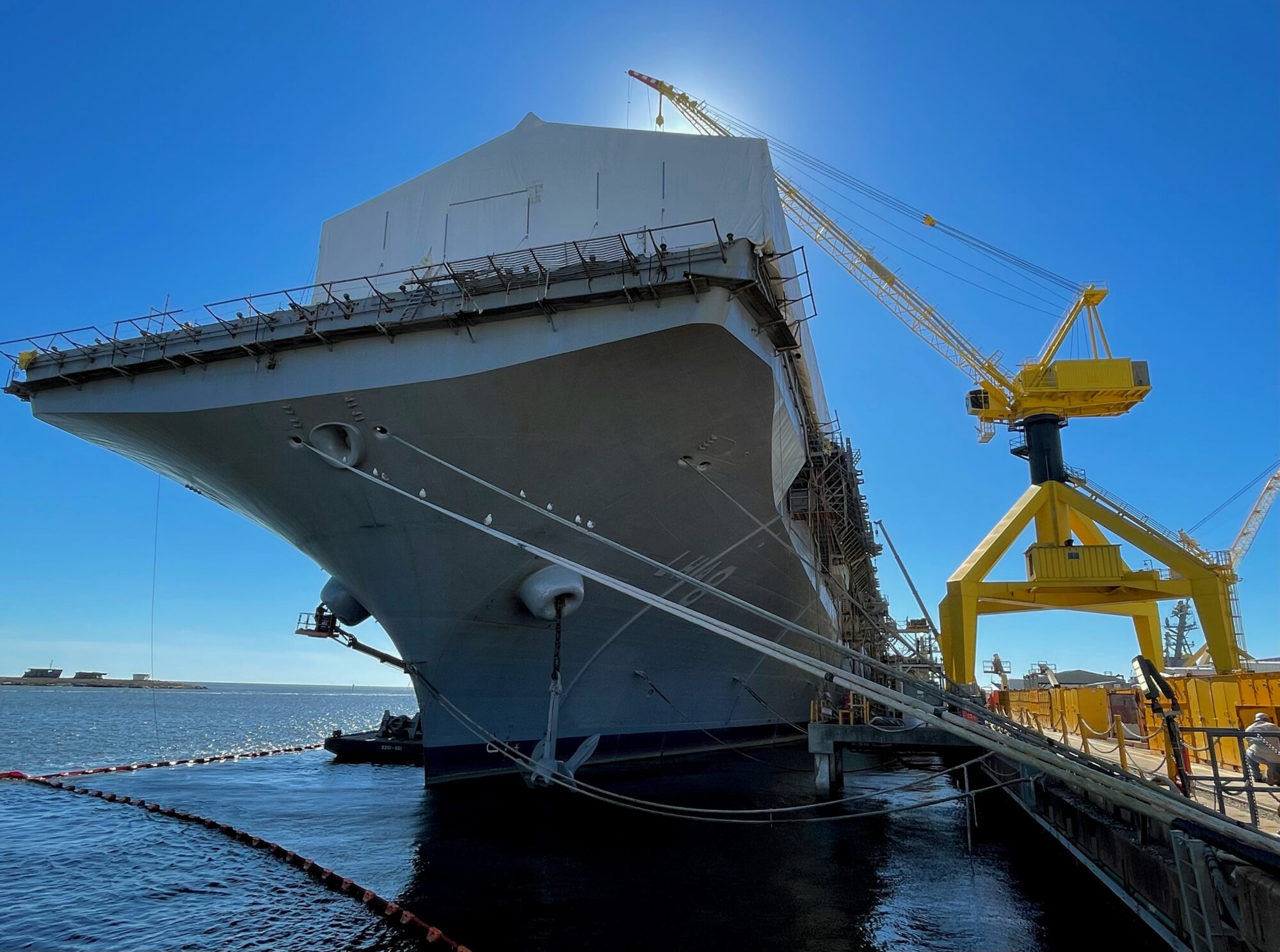
Photo of LHA8 at Ingalls on Nov. 20, 2024 (Photo: Frank Corder | Magnolia Tribune)
- A stronger maritime industrial base capable of fixing ships and getting them back into combat zones could be an important part of deterrence.
President-elect Trump’s incoming defense team will soon face a sobering fact: China’s navy is bigger than the U.S. Navy. “Our U.S. Navy shipbuilding is in a crisis and the U.S. Navy is dramatically shrinking, Sen. Dan Sullivan has said. By 2027, the U.S. Navy may be down to 280 ships while China’s navy hits 400.
China’s navy “has been on a historic trajectory these last 25 years,” according to ADM Samuel Paparo, Jr., commander of the U.S. Pacific Fleet. “We are not overmatched, but I don’t like the pace of the trajectory.”
The U.S. Navy must ramp up production. While investments in the shipyards are crucial, sparking a renaissance in Navy shipbuilding also depends on careful attention to the whole of the supplier base. Navy suppliers are found all over America. “We will not be successful in building these ships if we do not have the supplier base fully engaged and participating,” Navy Rear Admiral Todd Weeks, Program Executive Officer for Strategic Submarines, said on December 16. “There’s a lot more folks working in those suppliers than there are in the shipyards,” he noted.
While Weeks was referencing submarines, the statistics hold true for other ships. For example, the nuclear-powered Gerald R. Ford-class aircraft carrier taps a supplier base of parts built by over 2,000 businesses spread out across 44 states.
To catch up, the Navy must work this problem all along the supply chain, from advanced procurement through to the suppliers of fans, valves, motors and other fittings needed by a wide range of ships from aircraft carriers to amphibious warships.
Orders for big Navy ships start with advanced procurement and supplier problems can also begin with these specialized long-lead items. For example, a robust commercial market once supported castings and forgings. Then most of that work moved overseas, leaving primarily defense work in the U.S. market, which has become brittle, Weeks explained. “Castings seems to be the real sort of kink in the garden hose right now,” Rep. Joe Courtney, D-Conn., said last year. “There’s just not that many manufacturers that still do castings,” he added. “If you look at getting the cadence rate up to where I think everyone wants it to be, building out that supply chain infrastructure is really critical,” Courtney said.
To turn the problem around, the unique authorities for the new Columbia-class ballistic missile submarines are helping. “We decoupled material improvements from the contracts for the ships in order to accelerate getting work out to the industrial base,” Admiral Weeks said.
While the U.S. Navy and Congress focus on advanced procurement and the prime contractors, other suppliers are facing problems largely on their own. Take the example of axial fans used to vent engine rooms, workspaces, and living quarters. Their motors, impellers and casings must all meet Navy specifications for moving salt air and corrosive air containing small quantities of oil vapor and acid steam generated by battery evaporation. The fans have to pass tests for shock absorption and durability. Suppliers like American Fan, headquartered in Ohio, have fans on aircraft carriers and other vessels such as amphibious ships. Parent company Fairbanks Morse makes its own efforts to strengthen the industrial base, running a Defense Accelerator program to mentor small businesses with ideas and disruptive technologies applicable to defense.
Suppliers like these compete for workers, too, but without the special investments for other segments of the maritime industrial base. What suppliers need most is purchase orders and the stability to plan their future work, hiring and investment. Here, the decision to sustain a 31-ship amphibious fleet is helpful. A September 2024 contract award for three Flight II ships (LPD 33, LPD 34 and LPD 35) runs through September 2035, with work spread to Mississippi, Virginia, Wisconsin, Illinois, Massachusetts and other locations. That is the kind of stability needed for smaller firms supplying engines and other major parts.
In the end, the U.S. Navy depends on the men and women who build the ships. Washington, DC is abuzz with ways to address the ongoing challenge of wage inflation and retaining workers. The vast Newport News, Virginia shipyard is receiving $120 million from the Navy to upgrade parking, and the State of Virginia has added $40 million for new Navy housing and revitalized facilities.
Since 2018, the Submarine Industrial Base program has invested $2.3 billion in rebuilding capacity. Overall, the investments in supplier development covered 260 suppliers across 33 states and have netted a 20% improvement in production rate, Admiral Weeks said.
Don’t forget a dash of patriotism. Working on Navy ships is important, and it takes deep skills and dedication, often in real hot or cold weather. The security of this great nation (and dozens of allies) is at stake. America is proud of this awesome labor force.
The final reason for increasing maritime industrial-based capacity is sobering. These suppliers will be critical if U.S. Navy ships experience battle damage in the years ahead. Prepositioning parts at forward supply areas or onboard ships can help with maintenance and immediate repair. However, according to some wargame forecasts, the U.S. Navy might need significant battle damage repair capacity back in the United States. A stronger maritime industrial base capable of fixing ships and getting them back into combat zones could be an important part of deterrence.